-
December 19th, 2007, 01:54 AM
#61
Senior Hostboard Member
Originally posted by Steve Mac:
Now, I have another difficult decision which is how to fill the sides of the wedges to mount the side walls...this could laborious. I should just enjoy the moment...I've wondered how I was gonna cut this angle from day 1.
<font size="2" face="Verdana, Helvetica, sans-serif">Talking to myself today. Ah, I'm onto something now with attaching the sidewalls. All I really need is a product like this:
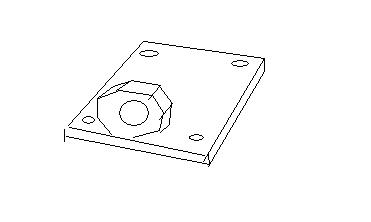
...then I could forget about filling the sides with wood and just attach these buggers to the wedge pieces. Oh geeesh I just saved myself a lot of work. Ideas?
-
December 20th, 2007, 03:22 AM
#62
Senior Hostboard Member
**** , no luck on finding something conceptually as simple as the nut orthogonal to a plate. Bizarre....I dunno what to do....**** ...yeah I could weld but **** ...I may as well cut more wood.
anyone here ever use these hurricane nuts instead of tee nuts?
-
December 20th, 2007, 03:48 AM
#63
Inactive Member
Coarse thread Sheetrock screws will hold driven into the edge grain of plywood. That and gorilla glue should work.
Jim N
-
December 20th, 2007, 03:57 AM
#64
Senior Hostboard Member
Used to be a product called Riv Nut. Was kind of a threaded pop rivet.
How bout a metal angled bracket and a irv nut? I 'll google to see if they are still around. there was a little hand set toll that was cheap...
-
December 20th, 2007, 03:58 AM
#65
Senior Hostboard Member
-
December 20th, 2007, 10:19 AM
#66
Inactive Member
Just make your flare panels overhang the wedges an inch or so on both the top and bottom, and run threaded rod through the overhang, clear across, side-to-side, on the rear of the wedges. If that's too industrial, slide on some polished tubing first. Pull the sides in as hard as you want. Use at least 5 rods each, top and bottom. Progessively space the rods closer from throat to mouth. If you're still using gaskets, they'd be easy to knock down too.
<font color="#FFFFFF" size="1">[ December 20, 2007 07:08 AM: Message edited by: bfish ]</font>
-
December 20th, 2007, 10:44 AM
#67
Inactive Member
If you slid 2 or 3 eyebolts on each of the rear crossrods as you put them in, you could attach the horn to the driver box too. Strong, forgiving, adjustable, and repeatedly undoable. No end-grain screws.
I'm thinking 1/4" rod for all but the rear, and 7/16" for them. Big washers or flat stock.
Nuts on both sides of everything to lock it once you get it.
If you started the rods at the throat, you could bolt your way forward, forming the flares as you go, and make (or mark) the final front cuts in place.
Sorry I can't autocad'd the concept (that IS a word in Tx, BTW). 
<font color="#FFFFFF" size="1">[ December 20, 2007 07:35 AM: Message edited by: bfish ]</font>
-
December 20th, 2007, 12:03 PM
#68
Inactive Member
...then just 3-5 more run vertically through-and-through to hold the high horn and stiffen the wedges...
-
December 20th, 2007, 12:21 PM
#69
Inactive Member
Just a hypothesis here...if you had a volume of steam rising up the flares as you drew them in, you might save some extra back-cutting, maybe even eliminate the need for it. Rigid rules.
Awhile back you mentioned 'having to be able to appreciate'...I'll bet about now...
You gotta appreciate how da#n big these things are!
-
December 20th, 2007, 01:30 PM
#70
Inactive Member
Can you steam bend plywood? They do make pre kerfed plywood just for this type application.
Jim N
Posting Permissions
- You may not post new threads
- You may not post replies
- You may not post attachments
- You may not edit your posts
-
Forum Rules
This forum has been viewed: 21281872 times.
Bookmarks